
For many car repair technicians and DIY enthusiasts, the process of disassembly and assembly of CV joints and ball cages is often accompanied by many challenges. The traditional manual method is not only time-consuming and laborious, but also easy to cause damage to parts due to improper operation, increasing unnecessary costs.
This is not a problem. By introducing advanced disassembly tools, the entire process can be made efficient and safe. Today we're going to delve into a powerful solution designed for this type of work-the 9-hole ball cage removal tool.
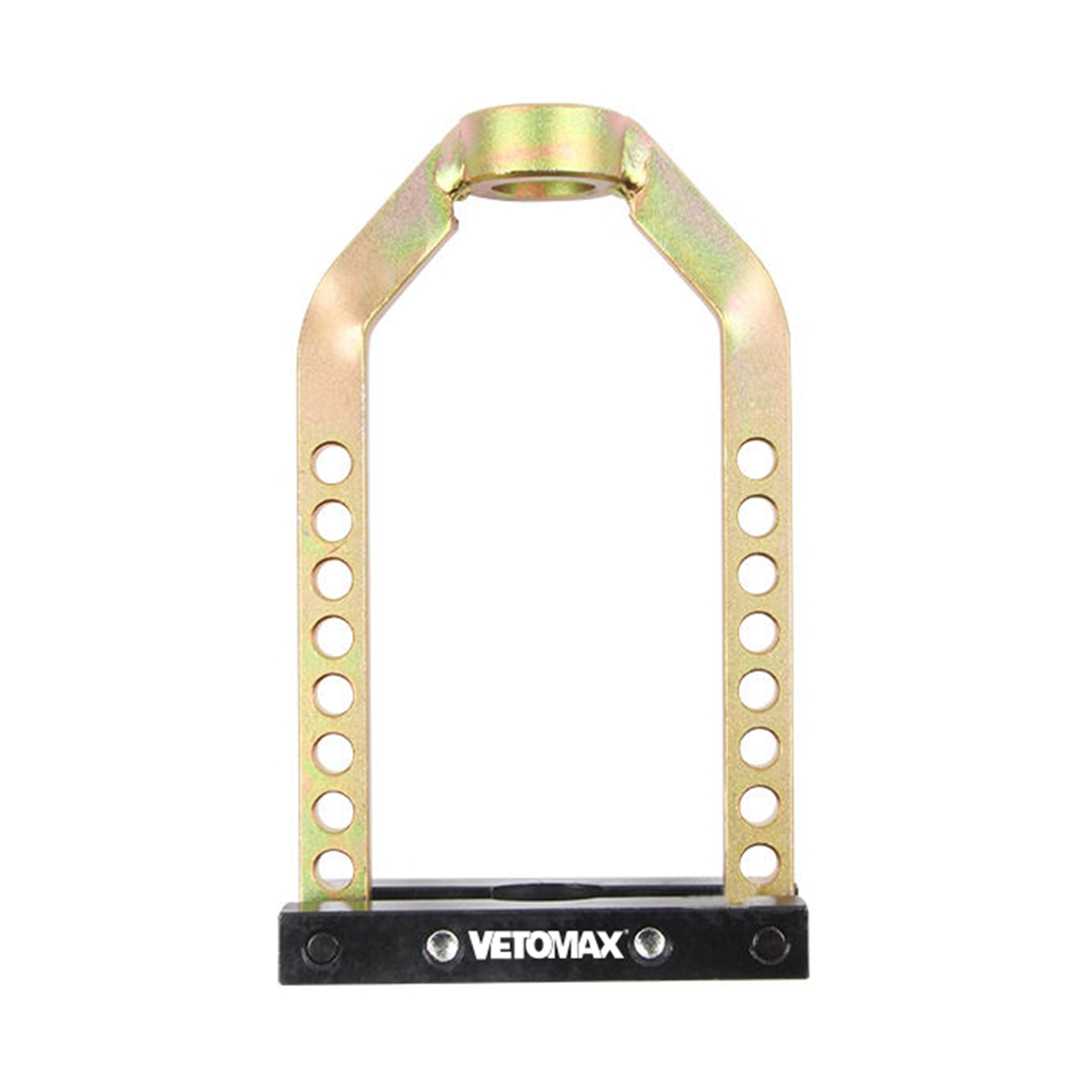
This 9-hole cage removal tool uses an innovative design concept that combines mechanical leverage with precision manufacturing. The user only needs to insert the tool into the specified position and apply the appropriate force to achieve perfect separation or fixation in an instant.
In addition, one of the biggest highlights of this product is that it can withstand an effective drawing distance of up to 100mm, which means that even the most complicated assembly situations are not a problem. Such powerful functionality makes every repair easy to carry out.
then how to use this artifact? first, we need to make clear the specific situation of the target area, and then push forward step by step according to the corresponding steps until all the procedures are completed.
Assuming that we want to replace a severely aged half-shaft assembly component, we can loosen the nut connector from one side and carefully remove the old part; then put the new spare parts in place and retighten all related parts to restore the original state and ensure that driving safety is fully guaranteed.
as a truly all-round equipment, this 9-hole ball cage removal tool has a very high degree of market adaptation. Whether you are a member of a team of professional technicians who focus on German luxury brand cars or a family craftsman who is keen on refitting Japanese and Korean small SUVs, you can benefit a lot from it.
This is because the manufacturer takes into account the differences between different models and conducts extensive testing and verification work on mainstream platforms during the development phase, thereby minimizing the possibility of potential risks.
When we compare the traditional method of freehand removal with the changes brought about by modern special equipment, the difference is obvious. The former usually takes a lot of time and energy to overcome problems such as frictional resistance, and there is also a risk of accidental injury to surrounding structures.
The latter greatly shortens the construction period and improves the quality standard line of finished products by virtue of precise positioning ability and uniform dispersion pressure. It can be said that this is a qualitative change level of leap-forward progress worthy of every practitioner's attention and try to see what the magic charm is!
of course, after having such a sharp weapon, it is necessary to pay attention to the daily maintenance links in order to give full play to the ideal effect for a long time ~ it is recommended to clean up the residual substances on the surface in time after each use so as not to corrode the metal material part; Regularly check the sufficient amount of lubricating oil at each movable joint to prevent the sticking phenomenon from affecting the next startup efficiency; in addition, the storage environment should also be dry and well ventilated to avoid adverse consequences such as corrosion hazards caused by wet weather.